赤い接着剤プロセス:
SMT Red Glueプロセスは、プレスまたはディスペンサーによって2つのパッドの間に満たされた赤い接着剤の熱い硬化特性を活用し、パッチとリフロー溶接で硬化させます。最後に、波のはんだ付けを通して、溶接プロセスを完了するための備品を使用することなく、波の頂上に表面マウント表面のみが波の頂上にあります。
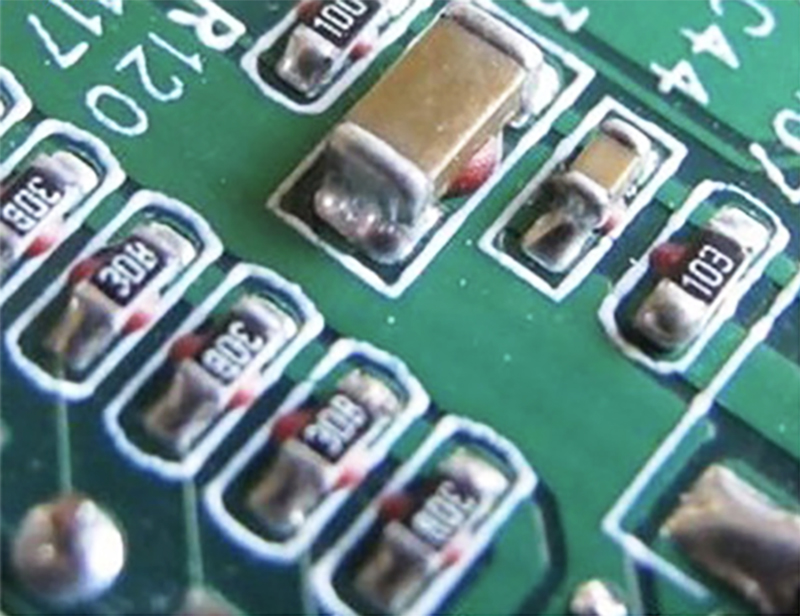
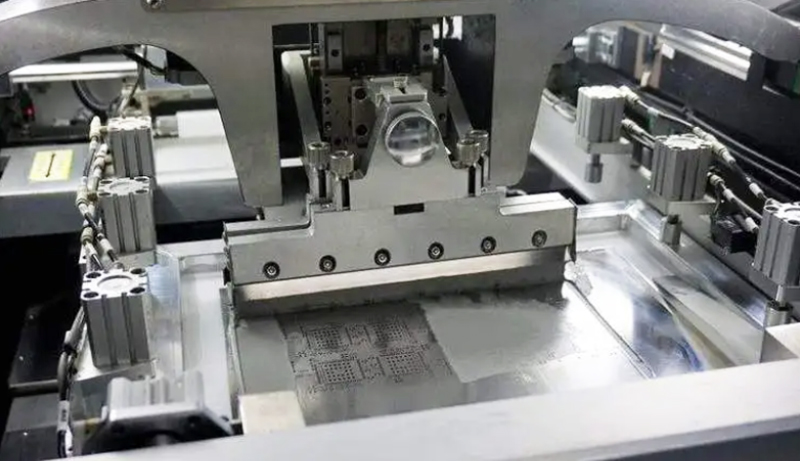
SMTはんだペースト:
SMTはんだペーストプロセスは、主に電子成分の溶接で使用されているSurface Mountテクノロジーの一種の溶接プロセスです。 SMTはんだペーストは、金属製スズパウダー、フラックス、接着剤で構成されており、優れた溶接性能を提供し、電子デバイスと印刷回路基板(PCB)間の信頼できる接続を確保できます。
SMTでの赤い接着剤プロセスの適用:
1.コストを測定します
SMT Red Glueプロセスの主な利点は、波のはんだ付け中に備品を作成する必要がないため、備品を作るコストを削減することです。したがって、コストを節約するために、少量の注文を行う顧客の中には、通常、PCBA処理メーカーが赤い接着剤プロセスを採用する必要がある顧客の一部が必要です。ただし、比較的後方溶接プロセスとして、PCBA処理プラントは通常、赤い接着剤プロセスを採用することに消極的です。これは、赤い接着剤プロセスが使用される特定の条件を満たす必要があり、溶接品質ははんだ貼り付け溶接プロセスほど良くないためです。
2.コンポーネントのサイズが大きく、間隔が広い
波のはんだ付けでは、表面に取り付けられたコンポーネントの側面が一般に頂上で選択され、プラグインの側面は上にあります。表面マウントコンポーネントのサイズが小さすぎると、間隔が狭すぎると、ピークが缶詰になるとはんだペーストが接続され、短絡が発生します。したがって、赤い接着剤プロセスを使用する場合、コンポーネントのサイズが十分に大きく、間隔が小さすぎてはならないことを確認する必要があります。
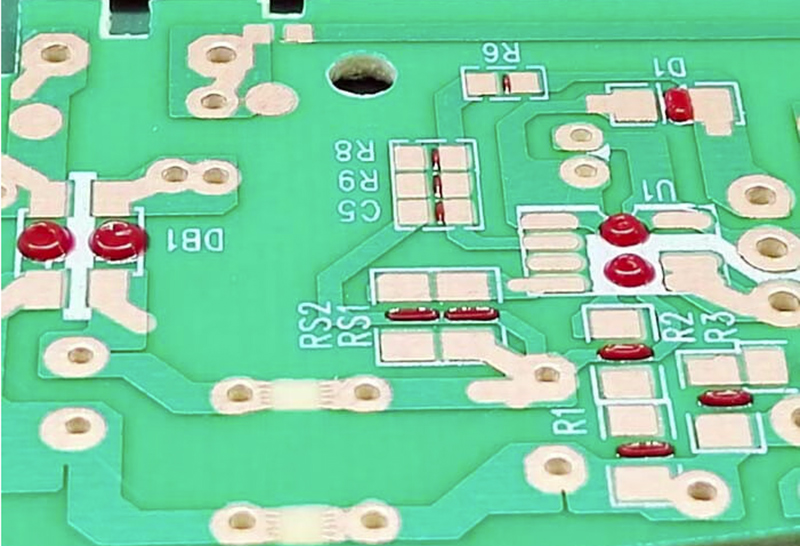
SMTはんだペーストと赤い接着剤プロセスの違い:
1。プロセス角
分配プロセスを使用すると、赤い接着剤は、より多くのポイントの場合、SMTパッチ処理ライン全体のボトルネックになります。印刷プロセスを使用すると、最初のAIとパッチが必要であり、印刷位置の精度が非常に高くなります。対照的に、はんだペーストプロセスには炉括弧の使用が必要です。
2。品質角度
赤い接着剤は、円筒形または硝子体のパッケージの部品を簡単に落とすことができ、貯蔵条件の影響下では、赤いゴム板は水分の影響を受けやすく、部品が失われます。さらに、はんだペーストと比較して、波のはんだ付け後の赤いゴム板の欠陥率は高く、典型的な問題には溶接の欠落が含まれます。
3。製造コスト
はんだペーストプロセスの炉ブラケットはより大きな投資であり、はんだジョイントのはんだのはんだペーストよりも高価です。対照的に、接着剤は赤い接着剤プロセスの特別なコストです。赤い接着剤プロセスまたははんだ貼り付けプロセスを選択するとき、次の原則が一般的に続きます。
●より多くのSMTコンポーネントとプラグインコンポーネントが少ない場合、多くのSMTパッチメーカーは通常はんだペーストプロセスを使用し、プラグインコンポーネントは後処理溶接を使用します。
●プラグインコンポーネントが増え、SMDコンポーネントが少ない場合、レッド接着剤プロセスが一般的に使用され、プラグインコンポーネントも後処理および溶接されます。どのプロセスを使用しても、目的は生産を増やすことです。ただし、対照的に、はんだペーストプロセスの欠陥率は低いですが、収量も比較的低くなっています。
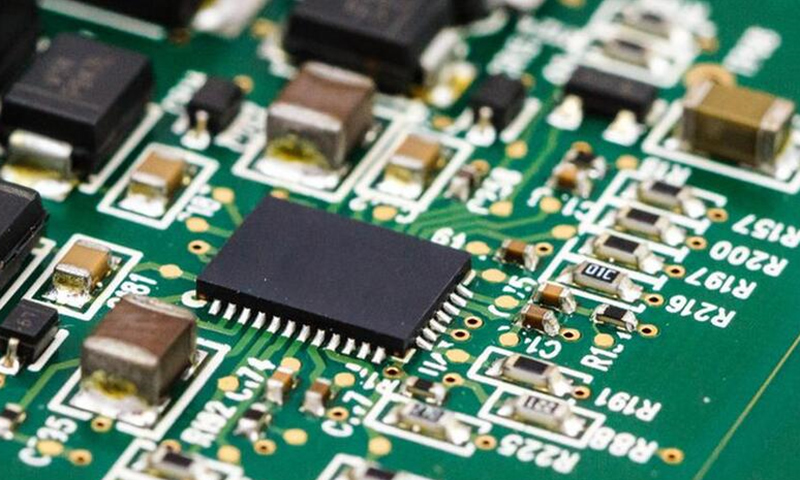
SMTとDIPの混合プロセスでは、片側逆流と波の紋章の二重炉の状況を回避するために、赤い接着剤がPCBの波の紋章溶接表面のチップ要素の腰に配置され、波の紋章溶接中にスズを1回適用し、ペーストペースト印刷プロセスを排除します。
さらに、赤い接着剤は一般に固定された補助的な役割を果たし、はんだペーストは実際の溶接の役割です。赤い接着剤は電気を導入しませんが、はんだ貼り付けは行います。リフロー溶接機の温度に関しては、赤い接着剤の温度は比較的低く、溶接を完了するために波のはんだ付けも必要ですが、はんだペーストの温度は比較的高くなります。