Etter at alt designinnholdet i PCB er designet, utfører det vanligvis nøkkeltrinnet i det siste trinnet - som legger kobber.
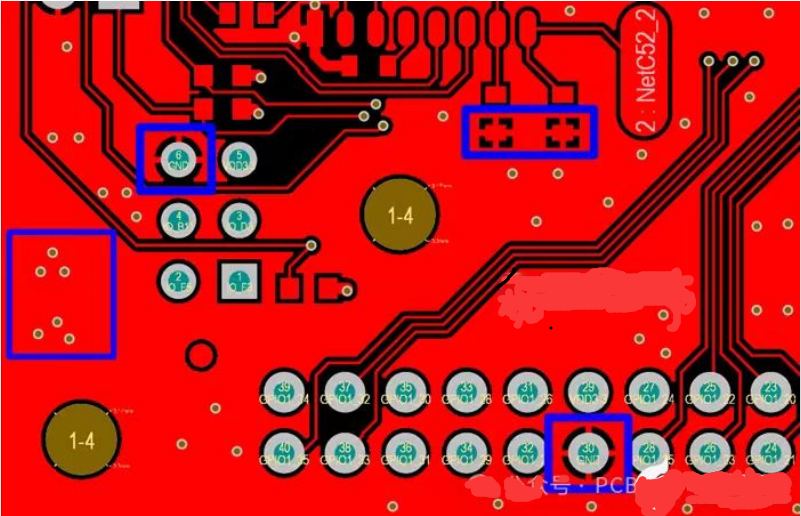
Så hvorfor lage det leggekobber på slutten? Kan du ikke bare legge den ned?
For PCB er rollen som kobberbelegg ganske mange, for eksempel å redusere bakkeimpedansen og forbedre anti-interferensevnen; Koblet til jordledningen, reduser sløyfeområdet; Og hjelp med kjøling, og så videre.
1, kan kobber redusere bakkeimpedansen, samt gi skjermingsbeskyttelse og støyundertrykkelse.
Det er mange topppulsstrømmer i digitale kretsløp, så det er mer nødvendig å redusere bakkeimpedans. Kobberlaging er en vanlig metode for å redusere bakkeimpedans.
Kobber kan redusere motstanden til jordtråd ved å øke det ledende tverrsnittsarealet med jordtråd. Eller forkorte lengden på jordtråden, redusere induktansen til jordtråden og dermed redusere impedansen til jordtråden; Du kan også kontrollere kapasitansen til jordtråden, slik at kapasitansverdien til jordledningen øker på riktig måte, for å forbedre den elektriske ledningsevnen til jordtråden og redusere impedansen til jordledningen.
Et stort område med bakke eller kraftkobber kan også spille en skjermingsrolle, og bidra til å redusere elektromagnetisk interferens, forbedre kretsens anti-interferensevne og oppfylle kravene til EMC.
I tillegg, for høyfrekvente kretser, gir kobberbelegg en komplett retursti for høyfrekvente digitale signaler, noe som reduserer ledningene til DC-nettverket, og forbedrer dermed stabiliteten og påliteligheten til signaloverføring.
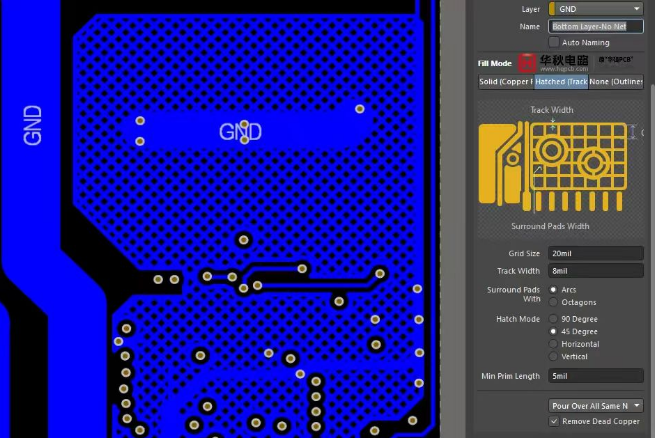
2, Legging av kobber kan forbedre varmedissipasjonskapasiteten til PCB
I tillegg til å redusere bakkeimpedans i PCB -design, kan kobber også brukes til varmeavledning.
Som vi alle vet, er metall lett å lede elektrisitets- og varmeledningsmateriale, så hvis PCB er asfaltert med kobber, øker gapet i brettet og andre blanke områder flere metallkomponenter, øker overflatearealet for varme, så det er enkelt å spre varmen til PCB -kortet som helhet.
Å legge kobber hjelper også med å fordele varmen jevnt, og forhindrer å skape lokalt varme områder. Ved å distribuere varmen jevnt til hele PCB -kortet, kan den lokale varmekonsentrasjonen reduseres, temperaturgradienten til varmekilden kan reduseres, og varmedissipasjonseffektiviteten kan forbedres.
Derfor, i PCB -design, kan legging av kobber brukes til varmeavledning på følgende måter:
Design varmeavledningsområder: I henhold til varmekildedistribusjonen på PCB -brettet, designer du med rimelig varmeavledningsarealer og legger nok kobberfolie i disse områdene til å øke varmedissipasjonsoverflaten og termisk konduktivitetsbane.
Øk tykkelsen på kobberfolie: Å øke tykkelsen på kobberfolie i varmedissipasjonsområdet kan øke den termiske konduktivitetsbanen og forbedre varmeavlederffektiviteten.
Design varmeavledning gjennom hull: Design varmeavledning gjennom hull i varmeavledningsområdet, og overfør varme til den andre siden av PCB -brettet gjennom hullene for å øke varmeavledningsveien og forbedre varmeavlederffektiviteten.
Tilsett kjøleribbe: Tilsett kjøleribbe i varmeavlederområdet, overfør varmen til kjøleribben, og forsvinner deretter varme gjennom naturlig konveksjon eller vifteavvik for å forbedre varmespredningseffektiviteten.
3, Legging av kobber kan redusere deformasjon og forbedre PCB -produksjonskvaliteten
Kobberbelegg kan bidra til å sikre enhetligheten av elektroplatering, redusere deformasjonen av platen under lamineringsprosessen, spesielt for tosidig eller flerlags PCB, og forbedre produksjonskvaliteten på PCB.
Hvis kobberfoliefordelingen i noen områder er for mye, og fordelingen i noen områder er for lite, vil det føre til ujevn distribusjon av hele brettet, og kobberet kan effektivt redusere dette gapet.
4, for å imøtekomme installasjonsbehovene til spesielle enheter.
For noen spesielle enheter, for eksempel enheter som krever jording eller spesielle installasjonskrav, kan kobberlaging gi ytterligere tilkoblingspunkter og faste støtter, noe som forbedrer enheten og påliteligheten til enheten.
Derfor, basert på fordelene ovenfor, vil elektroniske designere i de fleste tilfeller legge kobber på PCB -brettet.
Å legge kobber er imidlertid ikke en nødvendig del av PCB -design.
I noen tilfeller kan det ikke være passende å legge kobber. Her er noen tilfeller der kobber ikke skal spres:
A), Høyfrekvente signal linje:
For signallinjer med høy frekvens kan legging av kobber introdusere ytterligere kondensatorer og induktorer, noe som påvirker transmisjonsytelsen til signalet. I høyfrekvente kretsløp er det vanligvis nødvendig å kontrollere ledningsmodus for jordtråden og redusere returbanen til jordtråden, i stedet for å overføre kobber.
For eksempel kan det å legge kobber påvirke en del av antennesignalet. Å legge kobber i området rundt antennen er lett å forårsake signalet samlet av svakt signal for å få relativt stor interferens. Antennesignalet er veldig strengt for forsterkerkretsparameterinnstillingen, og impedansen til å legge kobber vil påvirke ytelsen til forsterkerkretsen. Så området rundt antenneseksjonen er vanligvis ikke dekket med kobber.
B), Høytetthetskretsbrett:
For kretskort med høy tetthet kan overdreven kobberplassering føre til kortslutning eller bakkeproblemer mellom linjene, noe som påvirker den normale driften av kretsen. Når du designer kretskort med høy tetthet, er det nødvendig å designe kobberstrukturen nøye for å sikre at det er tilstrekkelig avstand og isolasjon mellom linjene for å unngå problemer.
C), varmeavvisning for raskt, sveisevansker:
Hvis pinnen til komponenten er fullt dekket med kobber, kan det føre til overdreven varmeavledning, noe som gjør det vanskelig å fjerne sveising og reparasjon. Vi vet at den termiske ledningsevnen til kobber er veldig høy, så uansett om det er manuell sveising eller reflowsveising, vil kobberoverflaten lede varme raskt under sveising, noe som resulterer i tap av temperatur som loddejern, som har innvirkning på sveising, så designen så langt som mulig å bruke "tverrmønster" for å redusere varmeavfall og fasilitering av weld.
D), Spesielle miljøkrav:
I noen spesielle miljøer, for eksempel høy temperatur, høy luftfuktighet, etsende miljø, kan kobberfolie bli skadet eller korrodert, og dermed påvirke ytelsen og påliteligheten til PCB -brettet. I dette tilfellet er det nødvendig å velge riktig materiale og behandling i henhold til de spesifikke miljøkravene, snarere enn overleggende kobber.
E), spesialnivået på styret:
For det fleksible kretskortet, stivt og fleksibelt kombinert brett og andre spesielle lag i brettet, er det nødvendig å legge kobberdesign i henhold til de spesifikke kravene og designspesifikasjonene, for å unngå problemet med fleksibelt lag eller stivt og fleksibelt kombinert lag forårsaket av overdreven kobberopplegg.
For å oppsummere, i PCB-design, er det nødvendig å velge mellom kobber og ikke-kobber i henhold til spesifikke kretsskrav, miljøkrav og spesielle applikasjonsscenarier.