After all the design content of the PCB is designed, it usually carries out the key step of the last step - laying copper.
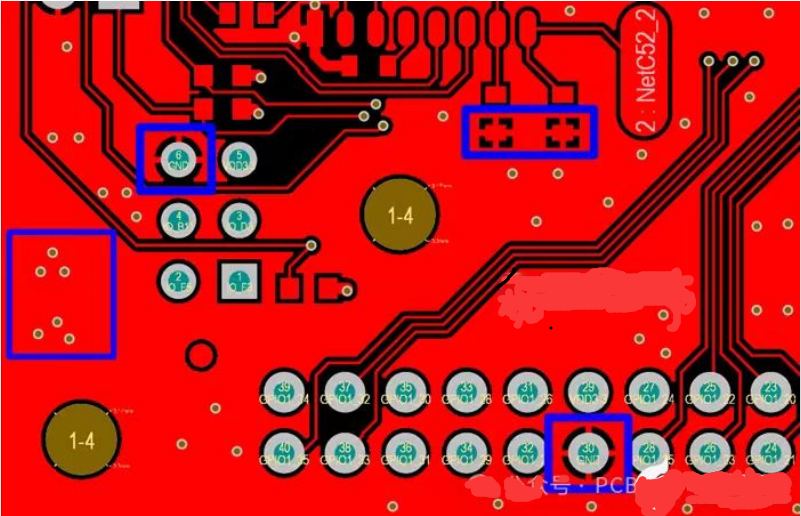
So why make the laying copper at the end? Can't you just lay it down?
For PCB, the role of copper paving is quite many, such as reducing the ground impedance and improving the anti-interference ability; Connected with the ground wire, reduce the loop area; And help with cooling, and so on.
1, Copper can reduce the ground impedance, as well as provide shielding protection and noise suppression.
There are a lot of peak pulse currents in digital circuits, so it is more necessary to reduce ground impedance. Copper laying is a common method to reduce ground impedance.
Copper can reduce the resistance of ground wire by increasing the conductive cross-sectional area of ground wire. Or shorten the length of the ground wire, reduce the inductance of the ground wire, and thus reduce the impedance of the ground wire; You can also control the capacitance of the ground wire, so that the capacitance value of the ground wire is appropriately increased, so as to improve the electrical conductivity of the ground wire and reduce the impedance of the ground wire.
A large area of ground or power copper can also play a shielding role, helping to reduce electromagnetic interference, improve the anti-interference ability of the circuit, and meet the requirements of EMC.
In addition, for high-frequency circuits, copper paving provides a complete return path for high-frequency digital signals, reducing the wiring of the DC network, thereby improving the stability and reliability of signal transmission.
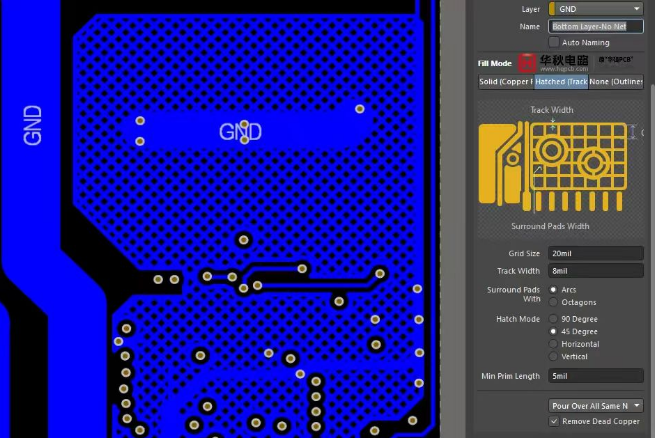
2, Laying copper can improve the heat dissipation capacity of PCB
In addition to reducing ground impedance in PCB design, copper can also be used for heat dissipation.
As we all know, metal is easy to conduct electricity and heat conduction material, so if the PCB is paved with copper, the gap in the board and other blank areas have more metal components, the heat dissipation surface area increases, so it is easy to dissipate the heat of the PCB board as a whole.
Laying copper also helps distribute heat evenly, preventing the creation of locally hot areas. By evenly distributing the heat to the entire PCB board, the local heat concentration can be reduced, the temperature gradient of the heat source can be reduced, and the heat dissipation efficiency can be improved.
Therefore, in PCB design, laying copper can be used for heat dissipation in the following ways:
Design heat dissipation areas: According to the heat source distribution on the PCB board, reasonably design heat dissipation areas, and lay enough copper foil in these areas to increase the heat dissipation surface area and thermal conductivity path.
Increase the thickness of copper foil: Increasing the thickness of copper foil in the heat dissipation area can increase the thermal conductivity path and improve the heat dissipation efficiency.
Design heat dissipation through holes: Design heat dissipation through holes in the heat dissipation area, and transfer heat to the other side of the PCB board through the holes to increase the heat dissipation path and improve heat dissipation efficiency.
Add heat sink: Add heat sink in the heat dissipation area, transfer heat to the heat sink, and then dissipate heat through natural convection or fan heat sink to improve heat dissipation efficiency.
3, Laying copper can reduce deformation and improve PCB manufacturing quality
Copper paving can help ensure the uniformity of electroplating, reduce the deformation of the plate during the lamination process, especially for double-sided or multi-layer PCB, and improve the manufacturing quality of the PCB.
If the copper foil distribution in some areas is too much, and the distribution in some areas is too little, it will lead to the uneven distribution of the entire board, and the copper can effectively reduce this gap.
4, to meet the installation needs of special devices.
For some special devices, such as devices that require grounding or special installation requirements, copper laying can provide additional connection points and fixed supports, enhancing the stability and reliability of the device.
Therefore, based on the above advantages, in most cases, electronic designers will lay copper on the PCB board.
However, laying copper is not a necessary part of PCB design.
In some cases, laying copper may not be appropriate or feasible. Here are some cases where copper should not be spread:
A), high frequency signal line:
For high frequency signal lines, laying copper may introduce additional capacitors and inductors, affecting the transmission performance of the signal. In high-frequency circuits, it is usually necessary to control the wiring mode of the ground wire and reduce the return path of the ground wire, rather than over-laying copper.
For example, laying copper can affect part of the antenna signal. Laying copper in the area around the antenna is easy to cause the signal collected by weak signal to receive relatively large interference. The antenna signal is very strict to the amplifier circuit parameter setting, and the impedance of laying copper will affect the performance of the amplifier circuit. So the area around the antenna section is usually not covered with copper.
B), high-density circuit board:
For high density circuit boards, excessive copper placement may lead to short circuits or ground problems between lines, affecting the normal operation of the circuit. When designing high-density circuit boards, it is necessary to carefully design the copper structure to ensure that there is sufficient spacing and insulation between the lines to avoid problems.
C), heat dissipation too fast, welding difficulties:
If the pin of the component is fully covered with copper, it may cause excessive heat dissipation, which makes it difficult to remove welding and repair. We know that the thermal conductivity of copper is very high, so whether it is manual welding or reflow welding, the copper surface will conduct heat rapidly during welding, resulting in the loss of temperature such as the soldering iron, which has an impact on welding, so the design as far as possible to use "cross pattern pad" to reduce heat dissipation and facilitate welding.
D), special environmental requirements:
In some special environments, such as high temperature, high humidity, corrosive environment, copper foil may be damaged or corroded, thus affecting the performance and reliability of the PCB board. In this case, it is necessary to choose the appropriate material and treatment according to the specific environmental requirements, rather than over-laying copper.
E), special level of the board:
For the flexible circuit board, rigid and flexible combined board and other special layers of the board, it is necessary to lay copper design according to the specific requirements and design specifications, to avoid the problem of flexible layer or rigid and flexible combined layer caused by excessive copper laying.
To sum up, in PCB design, it is necessary to choose between copper and non-copper according to specific circuit requirements, environmental requirements and special application scenarios.