In general: compared with the production process of multi-layer board and double-layer board, there are 2 more processes, respectively: inner line and lamination.
In detail: in the production process of double-layer plate, after the cutting is completed, drilling will be carried out, and then into the copper, the line; In the production process of multi-layer board, after the opening of the material is completed, it will not be directly drilled, but first it needs to go through the inner line and lamination, and then into the drilling workshop to drill, and then into the copper and the line.
That is, between the opening and drilling holes, two processes of "inner line" and "lamination" are added. The above is the difference between multi-layer board and double-layer board production.
Next, let's take a look at what the two processes of the inner line and lamination are doing
Inner line
The "line" process in the production of double-layer plates, including film compression, exposure, development (if you forget, you can go back and look at it).
The "inner circuit" here is not so simple! In addition to inner laminated film, inner exposure, inner development, it also includes inner pre-treatment, inner etching, inner film removal and inner AOI.
In the double-layer plate production process, the board after the copper deposition is completed, without the production line, directly into the pressing film, so there is no need to perform additional pre-pressing treatment. And the copper foil plate here, just came from the cutting workshop, the surface of the board will have impurities, so
Before the inner laminate film, it is necessary to advance the treatment and cleaning, the use of chemical reaction, first remove oil, water, clean water, two micro-etching (remove surface debris), and then water, and then pickling (after washing, the surface will be oxidized, so it needs pickling), then water, then dry, and then into the inner laminate film.
Inner laminate film before treatment
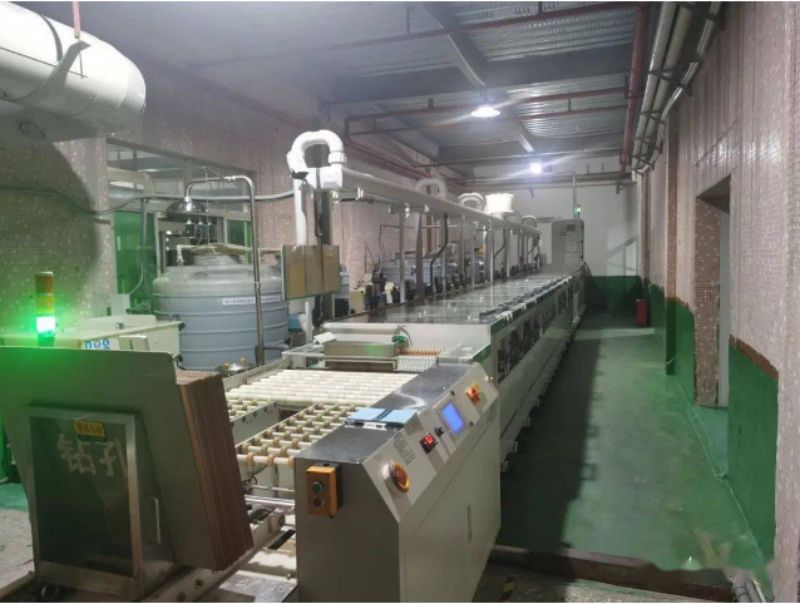
After pressing the board, because it has not been drilled, it looks very flat.
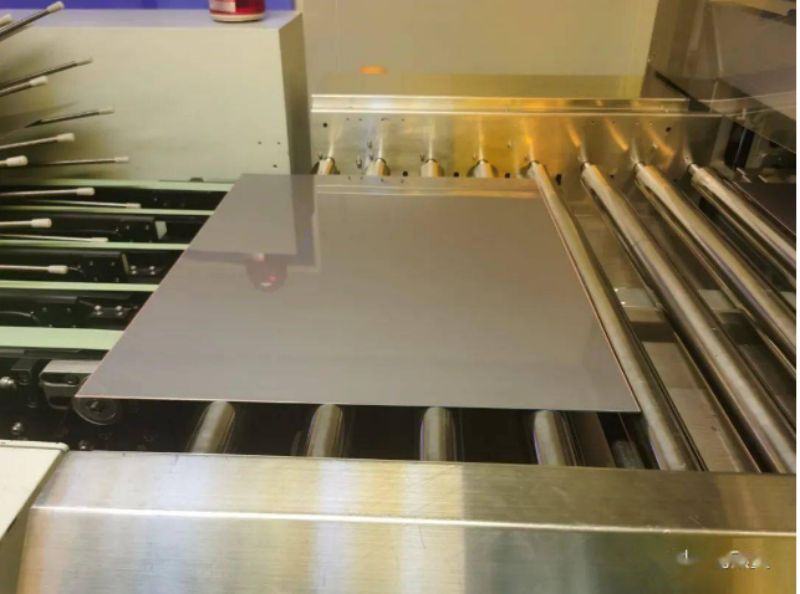
Pressing film, exposure, development, the specific matters of these links, have been introduced in the article of double-layer plate production, here will not be repeated.
After the development is completed, a part of the brass will be exposed, because the outer layer is a positive film process, the inner layer is a negative film process. Therefore, after the outer layer development is completed, the exposed line copper is the part that needs to be retained, and the copper exposed after the inner layer development is the part that needs to be etched off, so
The inner etching process and the outer etching process are also different, the inner etching is an alkaline process, at the time of etching, the dry film is still in, the part without the dry film (exposed copper) is etched off first, and then the mold is removed.
The etching of the outer layer is first removed and then etched, and the line is partially protected by liquid tin.
Inner film etching line, the left is responsible for etching, the right is responsible for film withdrawal.
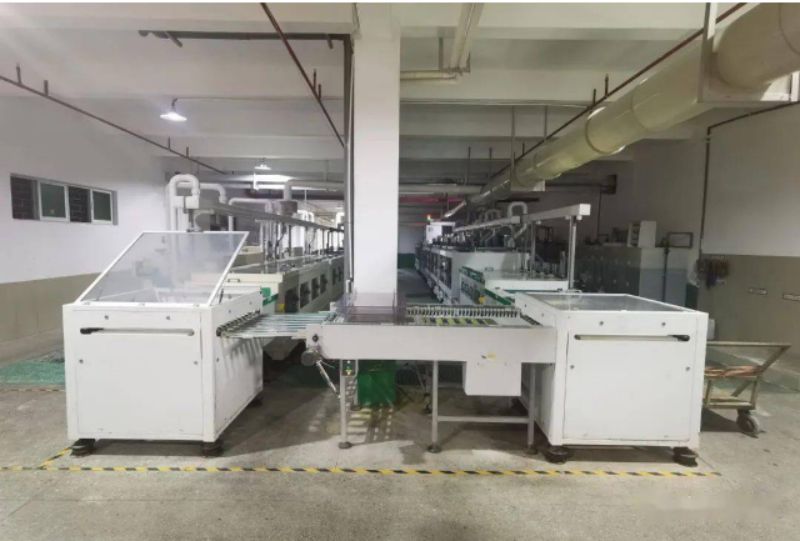
After etching the circuit board, the excess copper has been etched away, and the remaining part of the dry film has not been removed.
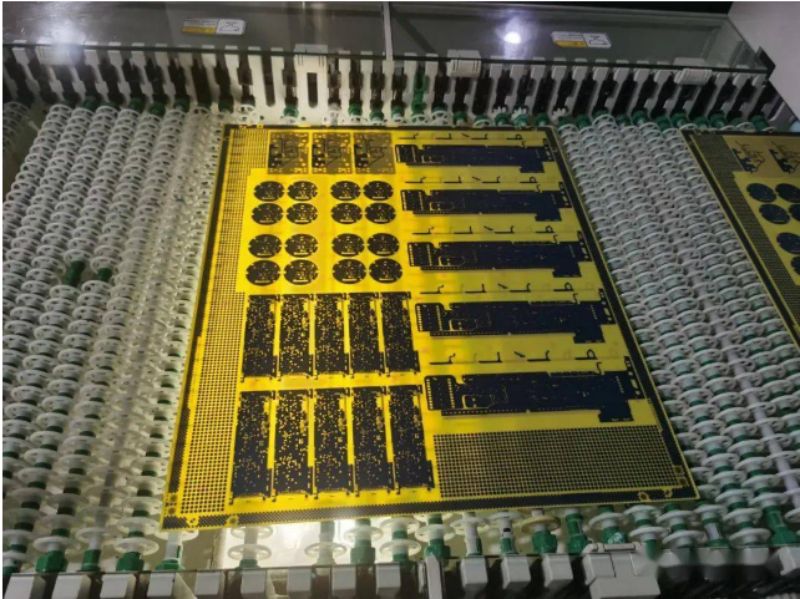
The circuit board after stripping.
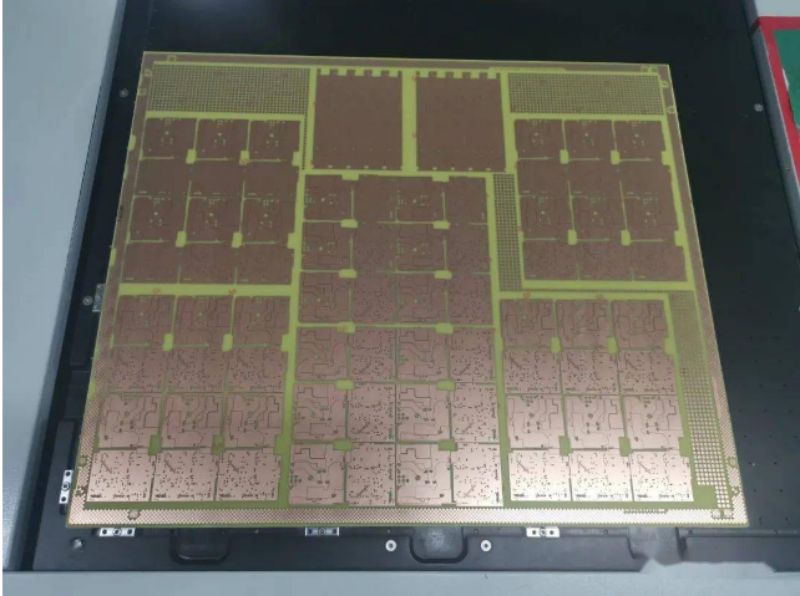
After the inner layer of the film is completed, the inner layer of the line is completely done, at this time, and then AOI optical detection, to determine that there is no problem, you can carry out the lamination process.
Lamination:
Just made the board, we call it the inner core board, if it is 4 layers of board, there will be 1 inner core board, if it is 6 layers of board, there will be 2 inner core boards.
The main purpose of this process is to make the inner core plate and the outer layer bonded together to form a whole. Responsible for the bonding material, called PP, Chinese called semi-curing sheet, the main composition is resin and glass fiber, it will also play the inner core board and the outer copper foil insulation purpose.
In order to ensure the quality of multi-layer board, the PP supplier of Jialichuang is still South Asia Electronics.
In general, the lamination process is divided into four steps in order: Browning, pre-stacking, platen, and pressing. Next, let's look at the details of each process separately.The inner core plate after the film removal is completed is browned first. The browned circuit board will add a layer of browned film on the surface of the circuit board, which is a brown metallized substance, and its surface is uneven, in order to make it easier to bond with PP.
The principle is similar to when repairing a bicycle tire, the broken place should be filed out with a file to improve the glue adhesion.
The Browning process is also a chemical reaction process, which will go through pickling, alkali washing, multi-channel washing, drying, cooling and other processes.
prelap
The pre-stacking process, carried out in a dust-free workshop, will stack the core plate and PP together. A PP is placed on each side of the core plate. The length and width of PP will be 2mm larger than the core plate to prevent hollow edges after pressing.
Raft:
The main purpose of the row plate is to add a layer of copper foil above the PP layer to prepare for the subsequent outer line. In addition, steel plate and kraft paper will be added to the outermost layer.lamination
The first few steps are to prepare for the final lamination.
Before laminating, in order to prevent warping, there will be a cover plate, about 12mm thick, steel.
Laminating includes two processes of hot pressing and cold pressing, respectively in the hot press and cold press. This is a very important link, to consider the factors including vacuum, temperature, pressure, time, these factors cooperate with each other, in order to produce high-quality circuit boards.
For example, in a certain period of time, how much temperature, how much pressure, and the length of time needed, should be precisely adjusted.
After the end of this process, the PP and the inner core plate and the outer copper foil will be closely connected together.
After coming out of the press, the automatic dismantling is carried out, the steel plate is removed, and it is sent to the platoon room again after grinding. As shown in Figure 11, the machine is removing the steel plate.
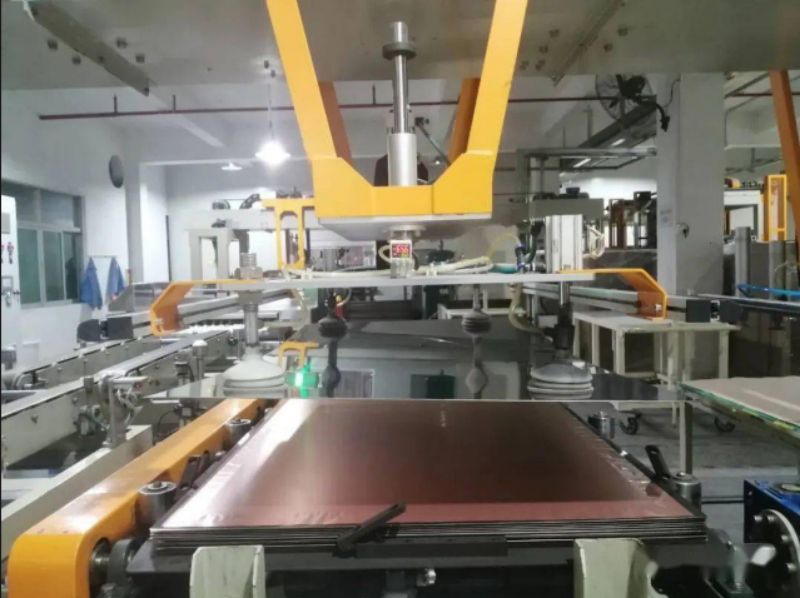
The laminated multi-layer circuit board will be returned to its original drilling workshop to drill, and the rest of the process is the same as the production process of the double-layer board.